JDodd
Well-Known Member
I'm needing some custom offset wheels and wanted to see if anyone has tried welding on a ring and bolting an aluminum center to it. If so what thickness did you use?
I did some simulations on my computer and using a .5" center and a 15,000 lb force there was .000629" distortion from a straight on force and the same 15,000 lb force applied to the side had a distortion of .001306".
From these simulations, .5" looks to be fine but personally it seems thin to me. So what do yall think, is it enough?
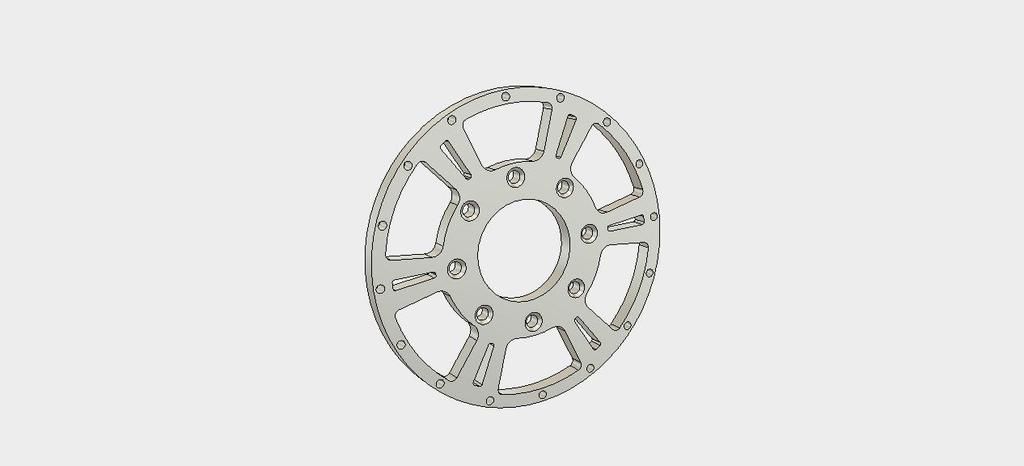
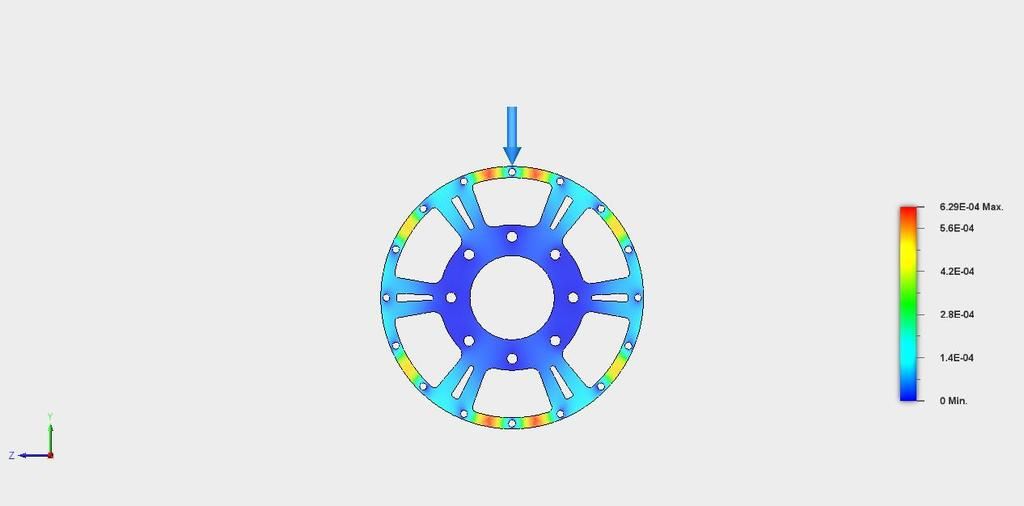

I did some simulations on my computer and using a .5" center and a 15,000 lb force there was .000629" distortion from a straight on force and the same 15,000 lb force applied to the side had a distortion of .001306".
From these simulations, .5" looks to be fine but personally it seems thin to me. So what do yall think, is it enough?
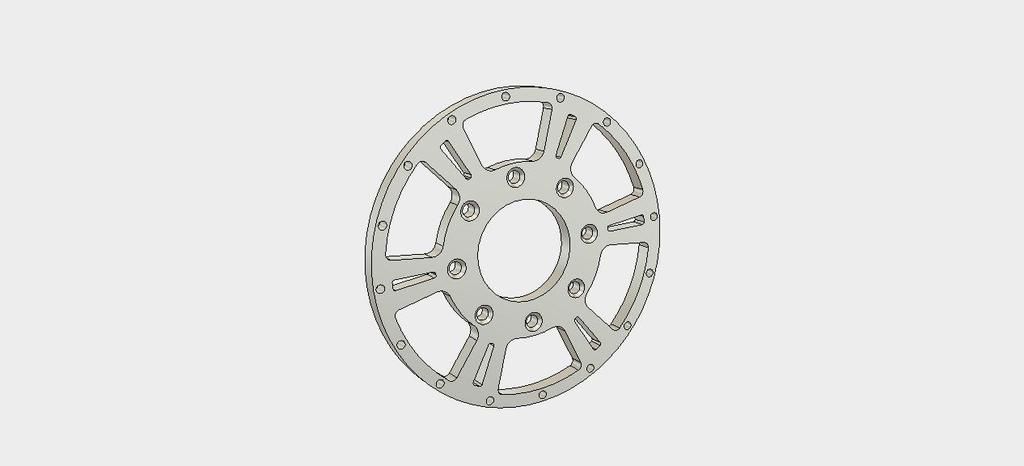
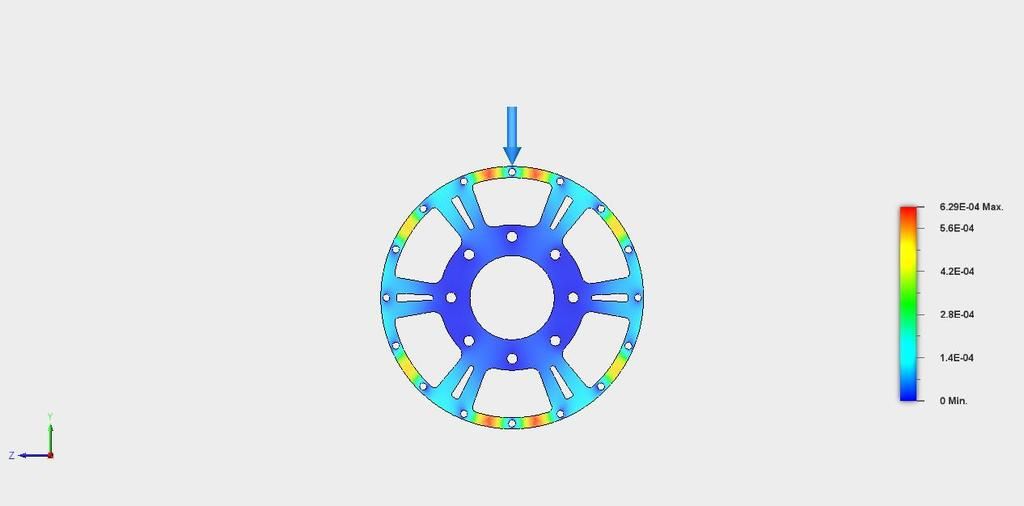
